Chuckanut Builders (located in Bellingham WA) recently posted a blog talking up one of it's projects making use of ThermaCork natural insulation! In the article, Chuckanut speaks to the natural qualities of ThermaCork, how it is being used in the "Community Energy Challenge," as well as how they wrapped the entire house! Definitely worth a look! We here at ThermaCork couldn't be prouder!
Corkhaus – Albert and Eva’s Cork-Clad Condo
Just shy of five years after Rob Hawthorne and Bart Berquist’s PDX Living LLC completed Corehaus , Portland’s first certified Passive House, Albert Rooks, owner of the Small Planet Workshop is nearing completion of his Corkhaus.
Albert has served on the board of directors of Passive House Northwest from its inception 5 years ago and provided incredible leadership within local, regional, and national passive house and green building communities including the NAPHN and the Northwest Ecobuilding Guild
With this EnerPHIt (Passive House Institute’s deep energy retrofit standard), Albert is walking his talk. Both on energy consumption and green building.
Making the Move
Last year, Albert and Eva put their lovely countryside home up for sale. This is sad in a way because we could always count on Albert and Eva to host PHnw board of director meetings in a lovely, comfortable setting in a space big enough for our 13 directors. However, the sale liberated them. No longer must they drive daily into Olympia from the countryside. And it allowed them to downsize into a small condo.
Even better, it allowed Albert to EnerPHit their new home. A nice cubic condo! And try many of the products he sells at Small Planet Workshop.
Uncovered exterior cork insulation
First, as the name suggests, their Corkhaus sports 3” of exterior cork insulation. Unfinished and uncovered. Completely exposed to the elements other than a modest roof overhang for the two story box. Sun, wind, and rain have already bleached the cork to a light tan, but over time Albert expects it will age it to a dark gray – almost black.
Opportunity?
Albert’s SPW sells this “ThermaCork” the Carbon Negatively processed, natural insulation imported from Portugal
Inspiration?
When he travelled to Portugal, Albert noticed that some buildings don’t cover the insulating cork but rely on air, wind, radiation, and warmth to dry it. He’ll try it!
Although the Prosoco FastFlash Albert applied under the ThermaCork provides a Weather Resistant Barrier protecting his condo’s sheathing, Albert believes that even in a Pacific Northwest climate, the Thermacork will shed water and dry.
He’s allowing RDH Building Sciences (Graham Finch and Robert Lapage) to monitor the backside of the Thermacork for evidence of moisture intrusion, and you can see the moisture probes inserted into the cork leading through the sheathing to the data collector.
You can see that Albert carefully overlapped the Thermacork panels so water entering the seams can drain down and out. This overlap also allowed him to hide the fastners for a cleaner appearance.
We’ll keep you posted on RDH Building Science’s findings.
CO2 Refrigerant Heat Pump Whole-house Heating
Second, Albert and Eva are only the second homeowners in North America trusting both their morning shower AND their space conditioning to a CO2-refrigerant heat pump water heater WITHOUT a backup electric resistance heater. Other than the stove/oven and lighting and appliances, Corkhaus has no heating source other than their Sanden Eco-System heat pump water heater.
Inspiration?
Just like the line of environmentally-superior building products Albert sells, Sanden’s CO2 refrigerant avoids the huge global warming footprint of conventional heat pump refrigerants.
Opportunity?
Albert’s been eager to try this new technology, and with WSU Extension Energy Program performing both laboratory testing and now field testing for Bonneville Power Administration conveniently from Ken Eklund’s office at the WSU in Olympia, Albert jumped at the opportunity to participate.
WSU is field testing Sanden’s CO2 Eco-System at four other locations, and interim field test reports are encouraging. However, none of those houses except Dan Welch’s home in Bellingham is a combi-system, providing both domestic hot water and space heating.
This presented another opportunity for Albert since he sells HRVs manufactured by Zehnder America Zehnder also owns Runtal, a manufacturer of high-quality radiators, and Albert and Eva will keep snug on winter nights with space heating from one Runtal radiator on each floor plus a tiny strip radiator in their bathroom.
Best of all, these slim radiators fit under Albert’s new Euroline windows revealing his stunning view of Puget Sound and Olympia’s waterfront.
lbert got his preliminary blower door result two weeks ago. It’s a promising 5 ACH.
This summer, he plans to airseal and superinsulate his roof (presently subinsulated with only R-11 fiberglass batts). Send him all of your ideas.
Science Projects: Tried at Home
Just 25 years after Dr. Feist started building the first passivhaus for his family (and 3 neighboring families) as a science experiment, Albert and Eva are taking part in two science experiments with their EnerPHit.
With their Corkhaus, they follow in the footsteps of many pioneers of energy-efficiency buildings.
Not only building science pioneers, they are in the subset of the bravest pioneers who experimented on their own families’ homes. For example, we’re in debt to Dr. Feist for the science experiment he started 25 years ago, And to Katrin Klingenberg for her passive home 12 years later.
Remember the old adage: “Don’t try this at home!” We’d not be as far along with passive house if people followed it.
Today, Albert and Eva are carrying on this fine tradition of experimenting. . . . in their own home.
We’ll keep you posted on his final blower door test.
Photos courtesy of Scott Means, Means Photography
Finished Facade
In our last post we told you to expect more photos soon. Well, now that the project is complete we have a few more photos of a beautiful facade for you! A close of up the fastening screws shows the method of attachment and a brilliantly understated rounding of the panel's edges gives this home a modern/natural feel. Surrounded by Tall trees, the facade seems to almost blend into it's setting.
Kriegh Architecture Studios Rounded Facade Paneling
This week Kriegh Artitecture Studios sent us an image of ThermaCork Facade Grade paneling, with one minute but very noticeable addition. They rounded the edges on all their boards! Julie Kreigh of Kriegh Architecture was quoted as saying "We wanted to go for a more consistent look."
Expect more photos of the Kriegh project soon!
High Performance Building with Natural Materials Symposium
We just got word that ThermaCork will be a featured topic of discussion at the Santa Cruz Natural Materials symposium held by Passive House California! The event is being held at the Resource Center for Non-Violence, Friday Februrary 20, 2015 from 9:00am to 1:00pm! Presenters include Bjørn Kierulf, a Norwegian architect, living in Slovakia, where he has designed and built over 70 Passive House buildings using naturally renewable and locally sourced straw, clay and wood-based materials. His company, Createrra, helped develop a Cradle to Cradle certified, panelized straw wall system, which he has used in multiple projects across Central and Eastern Europe. Andrew Michler, an author and builder who joins us from Colorado, where he has recently completed a Studio|Office|Guest House in high snow country, using a dense-packed cellulose, foam-free wall assembly. Andrew’s latest book, “(Ours) Hyperlocalization of Architecture,” published by eVolo Press, is a global tour of high performance and sustainable building. It covers Living Building Challenge and Passive House projects from Seattle to Australia to Germany and includes interviews with William McDonough, Edward Mazria and Wolfgang Feist and Rob Nicely, a Monterey artist and contractor and owner of Carmel Building and Design. His company has won multiple awards for sustainable design and has certified projects to LEED, Passive House and Living Building Challenge requirements. He’s currently focused on sourcing local, naturally based materials and avoiding anything on the Living Futures Institute’s ‘Red List.’
Learn all about how non-toxic and natural building materials are being used to achieve Passive House levels of performance for homes, schools and commercial buildings. Our panel of local and international experts will share examples of their work and discuss how their materials and methods can be implemented and adapted in our own buildings.
Date: Friday, February 20th
Time: 9.00am – 1.00pm (Includes Lunch)
Place: Resource Center for Nonviolence
612 Ocean Street, Santa Cruz, CA 95060
Cost: $45 for PHCA members, $65 for General Public,
SPACE IS LIMITED TO 55 SO RESERVE YOUR SEAT ASAP!
Birdsmouth Project
Birdsmouth Construction grew out of the passion for building well‐ designed, environmentally conscious living spaces that stand the test of time. They have embraced new technologies Like ThermaCork and building approaches like The Passiv-Haus Institute, while remaining true to their basic core principles of high quality materials, craftsmanship and personalized service. Whether they design your project or work with your architect’s plans, they are committed to helping turn your vision into reality and that is exactly what they have done with their new ThermaCork Facade grade project in Portland Oregon.
Founded in 2007 by General Contractor Joshua Salinger, Birdsmouth Construction is a residential and small commercial construction services firm with headquarters in southeast Portland. They serve clients throughout the Portland metro area, offering design, project development, project management, and construction. We take great pride in our work, and it shows. Their wide-ranging Portfolio includes kitchens, bathrooms, additions, dormers, finished basements, Accessory Dwelling Units, and custom homes!
Re-Declare(d)
Today ThermaCork was awarded the distinguished "Declare" certification for the second year in a row, making ThermaCork a leader in the transparent materials economy!
Human and environmental health considerations have emerged as a crucial factor in material selection. Declare is a Standardization for manufacturers of ecologically sound products to demonstrate Just how environmentally friendly they really are.
Declare is also the certification used by the Living Building Challenge. "widely accepted to be the most advanced green building standard in the world" to select products that meet the Living Building Challenge’s stringent materials requirements, streamlining the materials specification and certification process. The purpose of the Living Building Challenge is straightforward – it defines the most advanced measure of sustainability in the built environment possible today and acts to diminish the gap between current limits and ideal solutions.
To be considered for the Declare certification, an extremely through and stringent process must be undertaken of testing and tracing chemical elements. Thus making sure nothing from "The Red List" is present. The Red List represents the “worst in class” materials, chemicals, and elements known to pose serious risks to human health and the greater ecosystem. A "Living Building Project" cannot contain any of the following materials or compound.
Asbestos
Cadmium
Chlorinated Polyethylene and Chlorosulfonated Polyethlene
Chlorofluorocarbons (CFCs)
Chloroprene (Neoprene)
Formaldehyde (added)
Halogenated Flame Retardants
Hydrochlorofluorocarbons (HCFCs)
Lead (added)
Mercury
Petrochemical Fertilizers and Pesticides
Phthalates
Polyvinyl Chloride (PVC)
Wood treatments containing Creosote, Arsenic or Pentachlorophenol
We here at ThermaCork Proudly display our certification in our showroom, just as we are proudly displaying it here! Check out both Declare and Living Building challenge's websites in the links below!
Bellingham Cold Storage
Recently, we here at ThermaCork found an old abandoned cold storage locker in Bellingham, Washington. Upon further investigation, we found that the entire unit had been insulated using Cork! The Interior of the unit had discarded items strewn about haphazardly, really showing the age of the unit itself and how long it had been since it was actively utilized as a Cold Storage Room. However, the Cork Insulation was holding up beautifully! Parts of the interior wall and moldings had fallen off, exposing the Cork Insulation (which we've pointed out with Red arrows) but the Cork itself looks nearly brand new! This Juxtaposition between the Cork and the Items in the room and the wall treatments, really shows off Cork's proven ability to stand the test of time!


"Shelter byGG" Brings MOD to Modular
Portuguese artist and designer Gabriela Gomes has designed "Shelter byGG" a sculptural habitable module. The module is an experimental object, a "cocoon/bedroom" which seeks to give the user an unexpected experience of a living space. According to the architect, it allows for "new experiences with space" and questions the "relations of artistic enjoyment and habitation issues."
The module features ThermaCork Insulation throughout, Denoting environmental concerns. This MODular shelter also uses solar energy and LED lighting.
When you are ready to move locales, all one has to do is simply rent a flatbed truck and you are up and ready to install your Shelter in a new location.
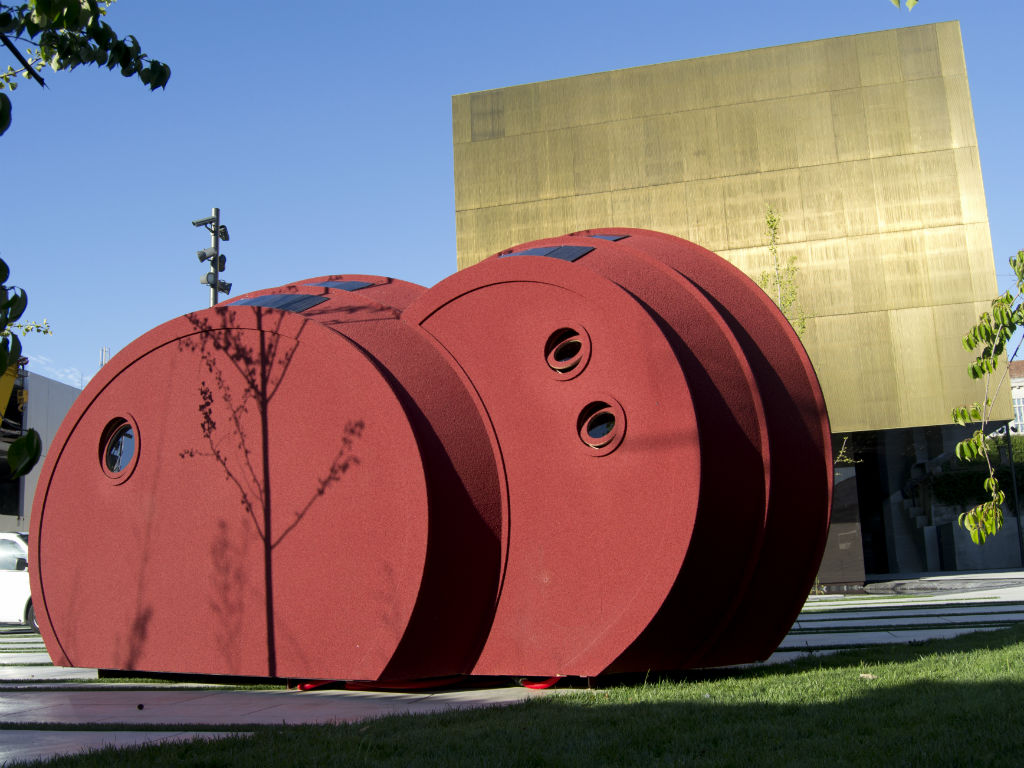
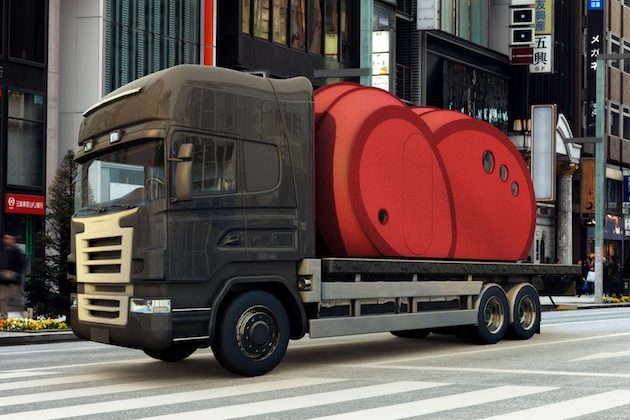





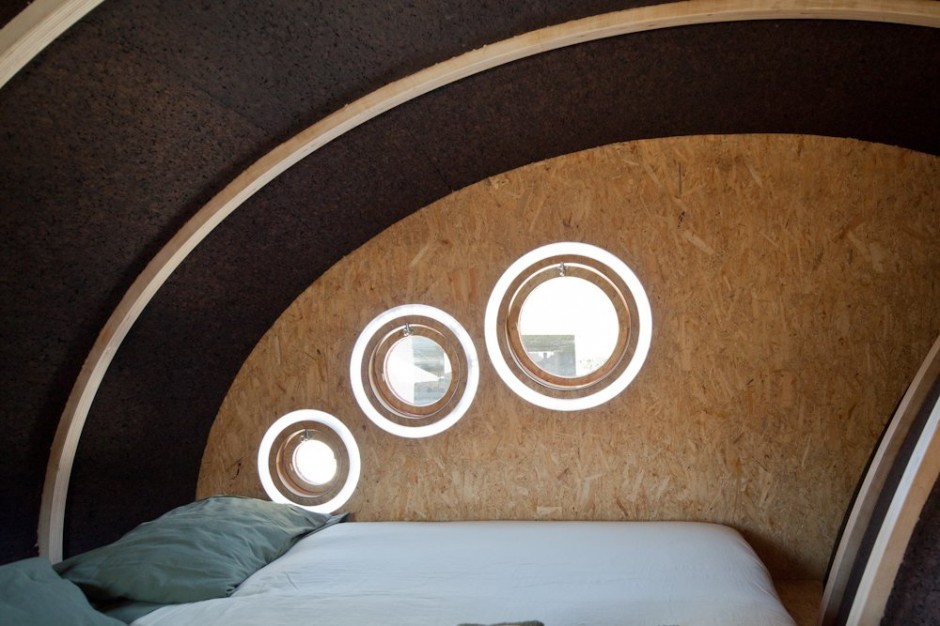


Dwell Development's Corky New Project
The Seattle-based sustainable building company Dwell Development is currently building the Northwest's first Net Zero/Passive Homes featuring ThermaCork facade. Purchased from The Small Planet Workshop, the award-winning ThermaCork is used as exterior insulation visible on the front of two homes located in Columbia City's BLOCK34 and BLOCK35 communities. The use of ThermaCork is not only visually appealing, but the material also has a negative carbon footprint and adds to the already super insulated building envelope. The homes are solar ready, and additional features include triple pane high-performance windows and recycled and reclaimed materials.
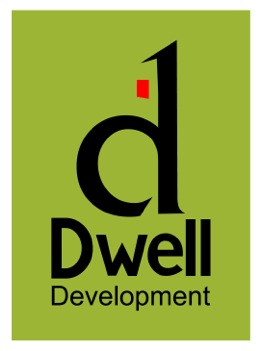
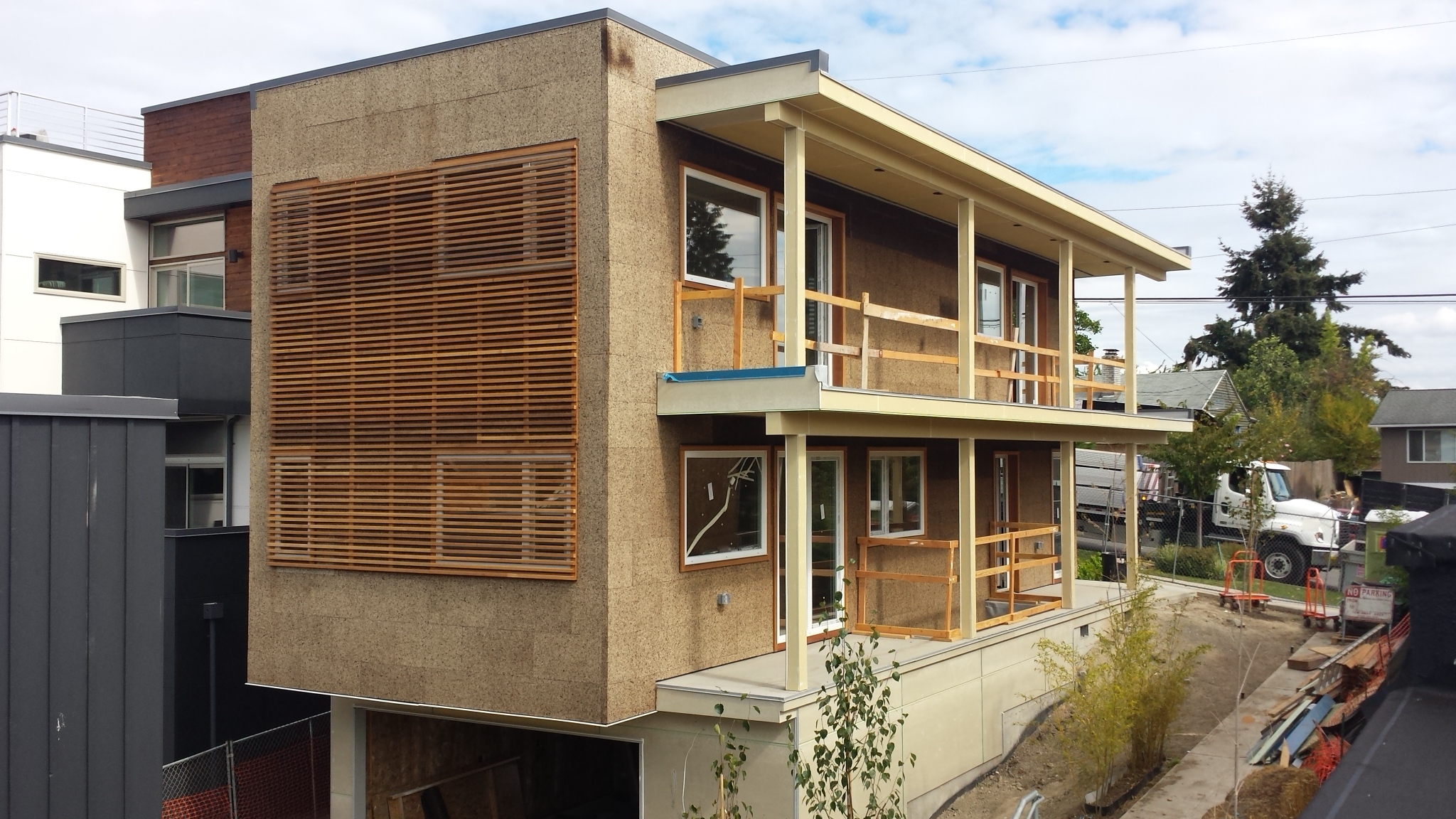

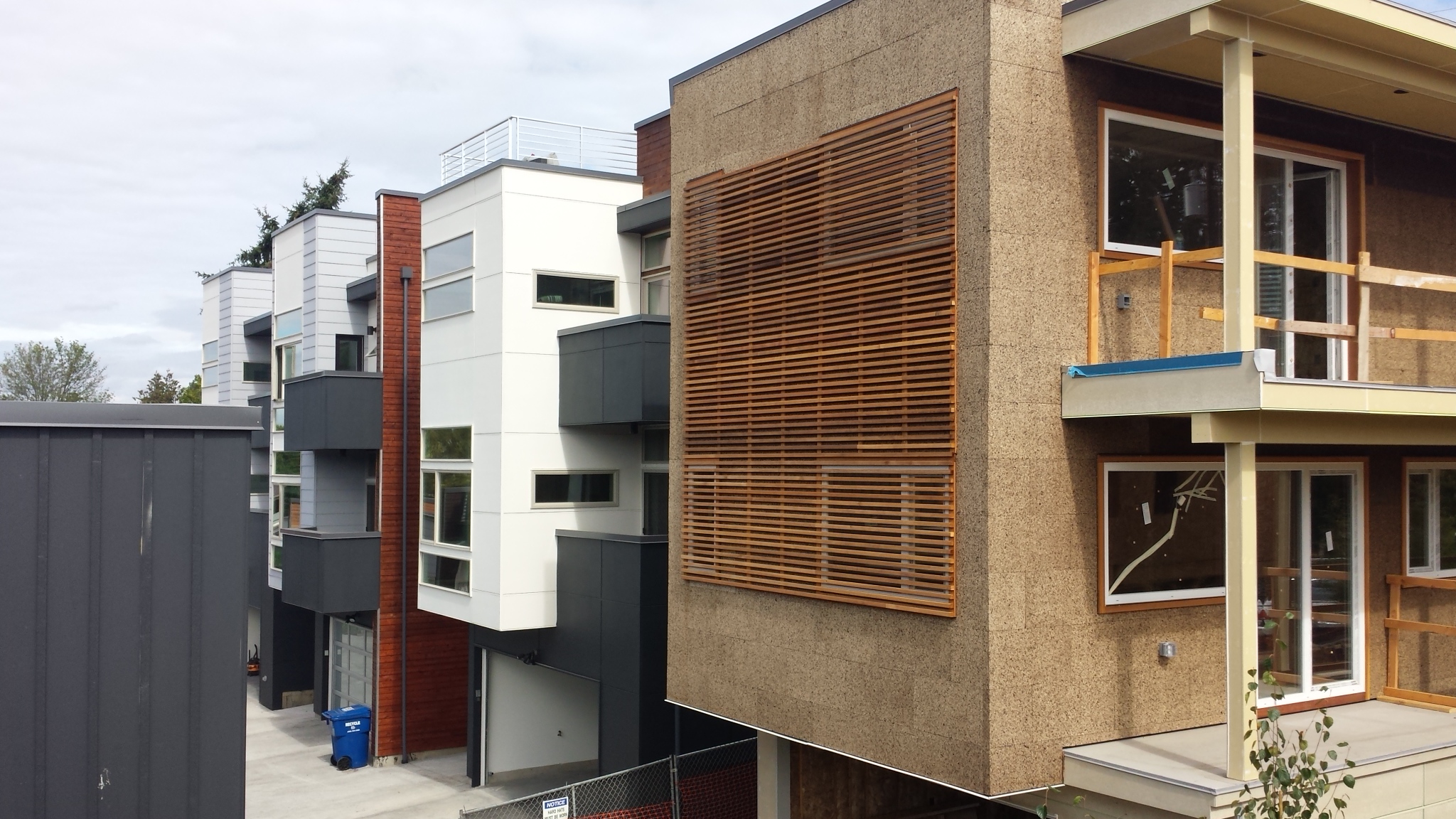
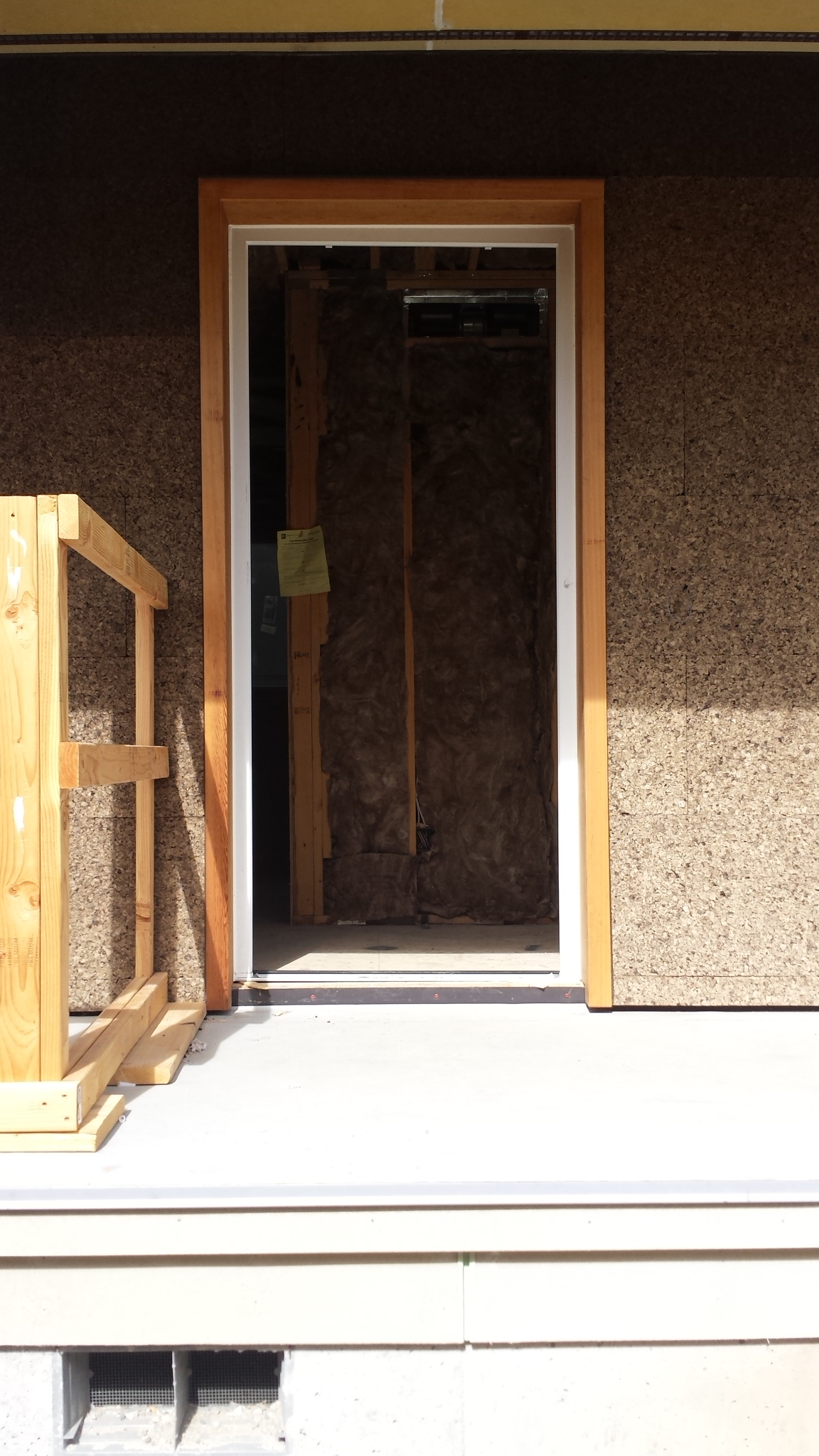
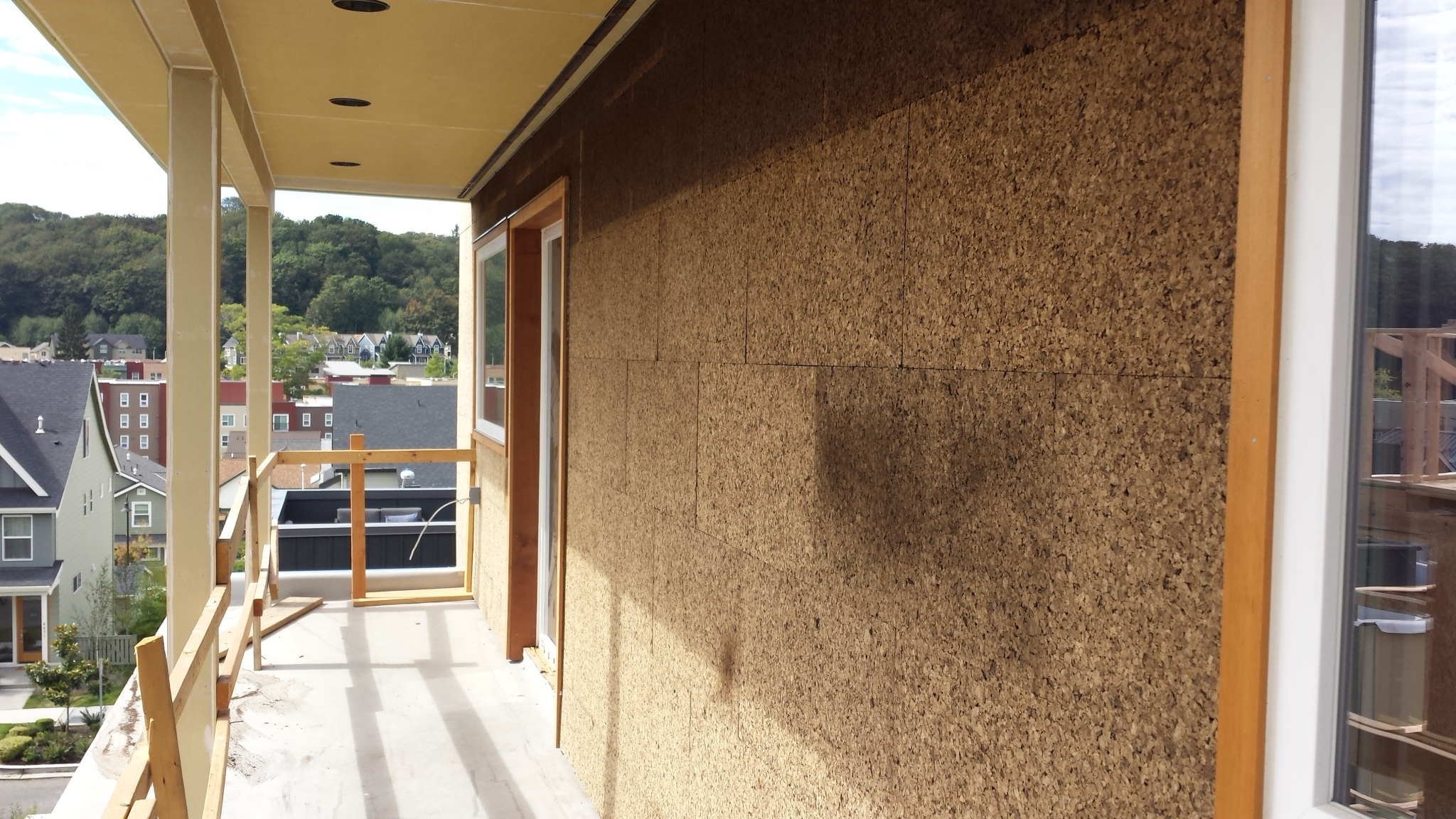
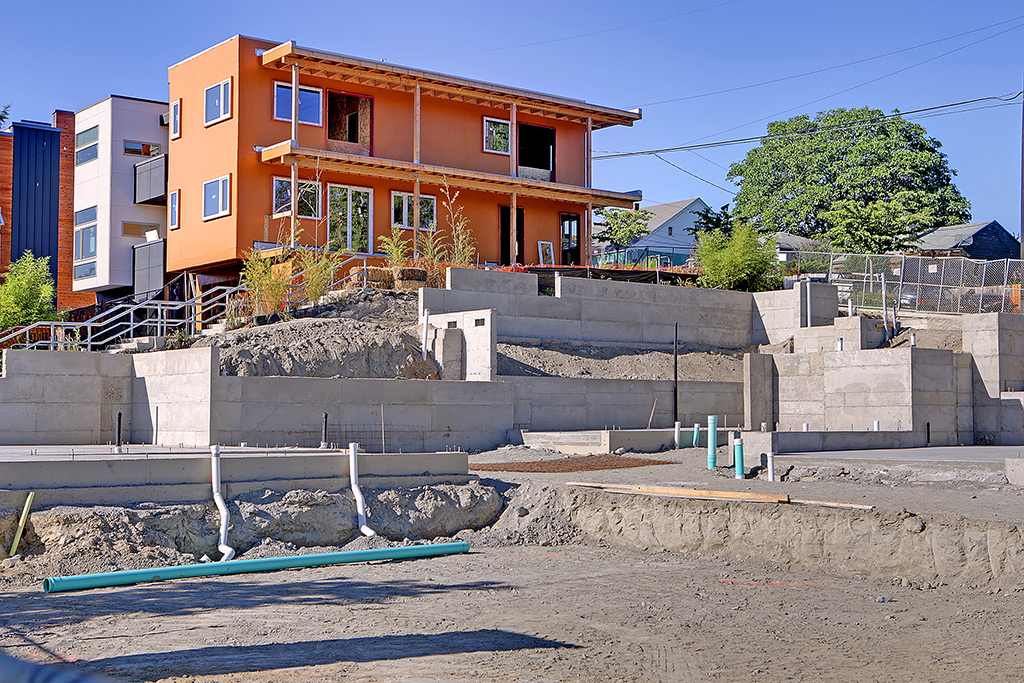
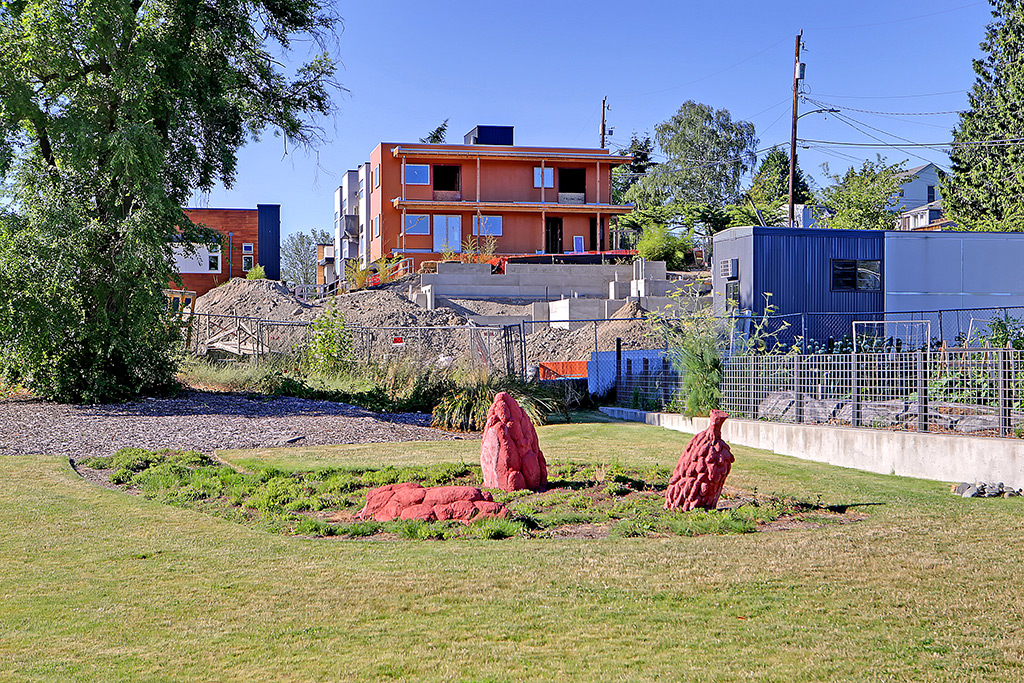
Philadelphia's POP Project
An environmentally-friendly real estate developer is nearly finished two quirky, or better yet... corky, homes in Philadelphia that are the first of their kind in the United States.
Located in the city’s Kensington neighborhood, the Pop Project is two 3-bedroom, 2.5-bath buildings which boast a unique cork façade, which also acts as insulation for the nearly 2,000-square-foot houses. It is a natural product that is carbon negative, meaning it actually reduces the level of carbon being used in the world.
Architecture firm Orange Concept did not include the façade on the ground floor's exterior to avoid damage from passers-by. Cork, which can sustain wind, rain and other natural elements, creates a stronger sound barrier than more commonly used materials and reduces heating and cooling costs since it super insulates the homes.
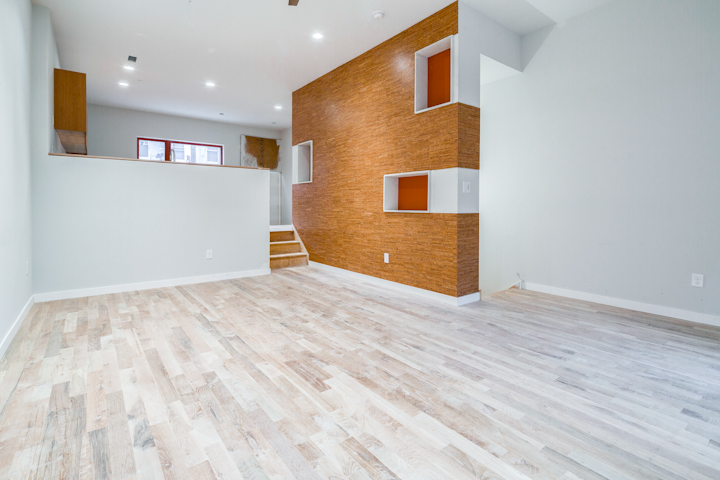
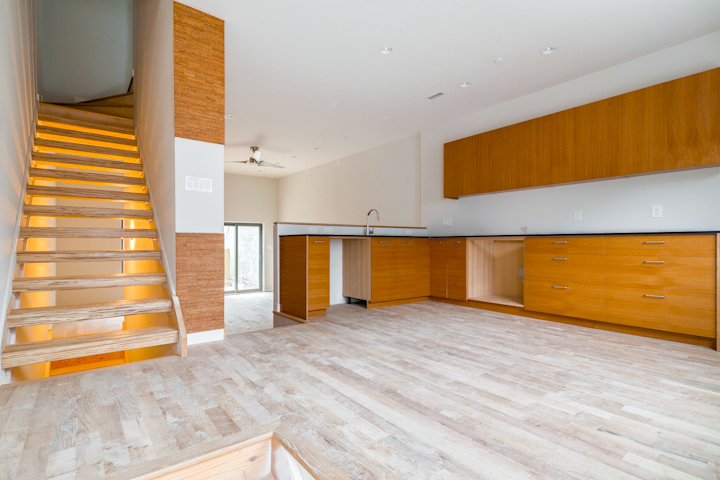
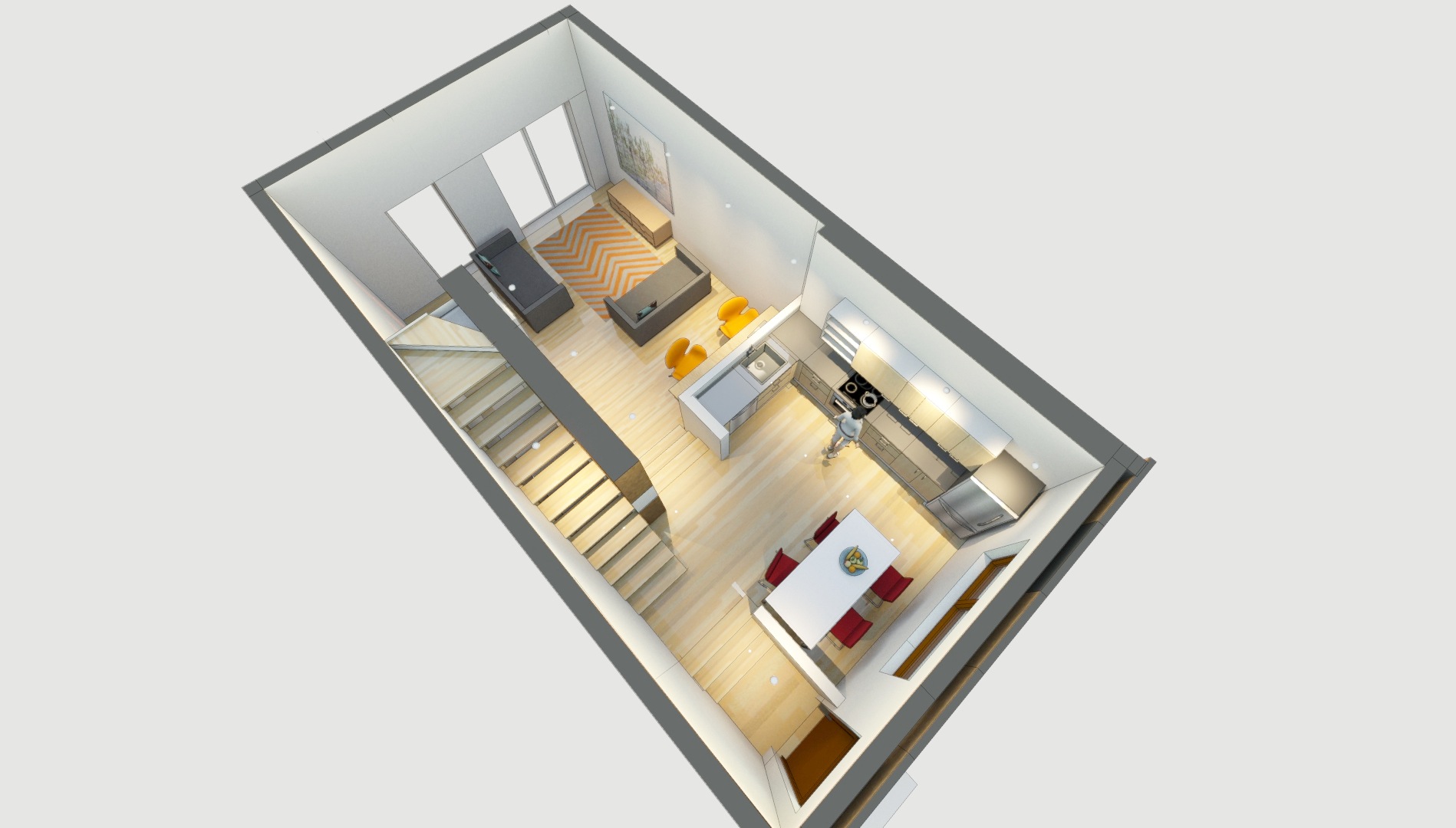
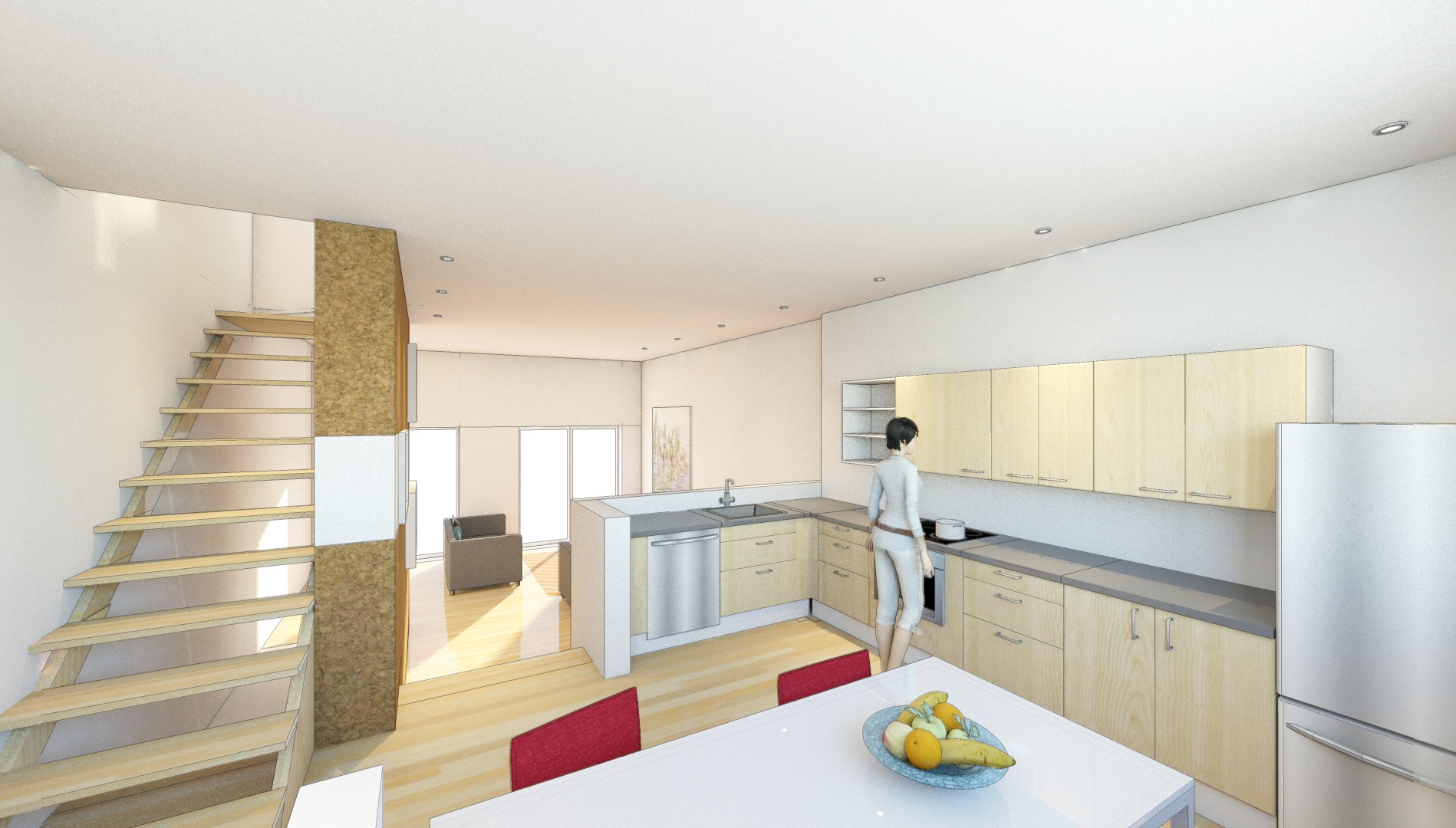
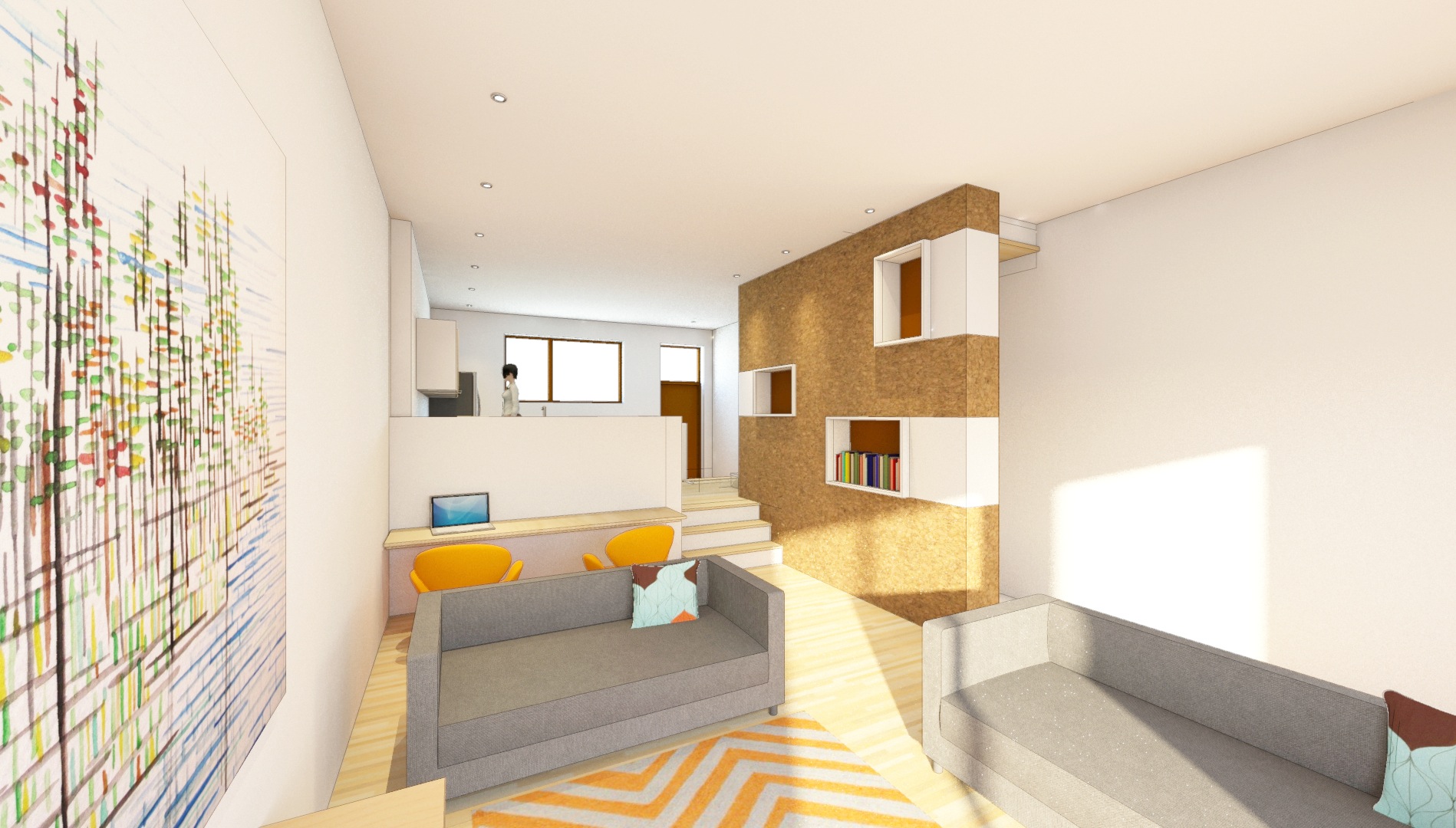
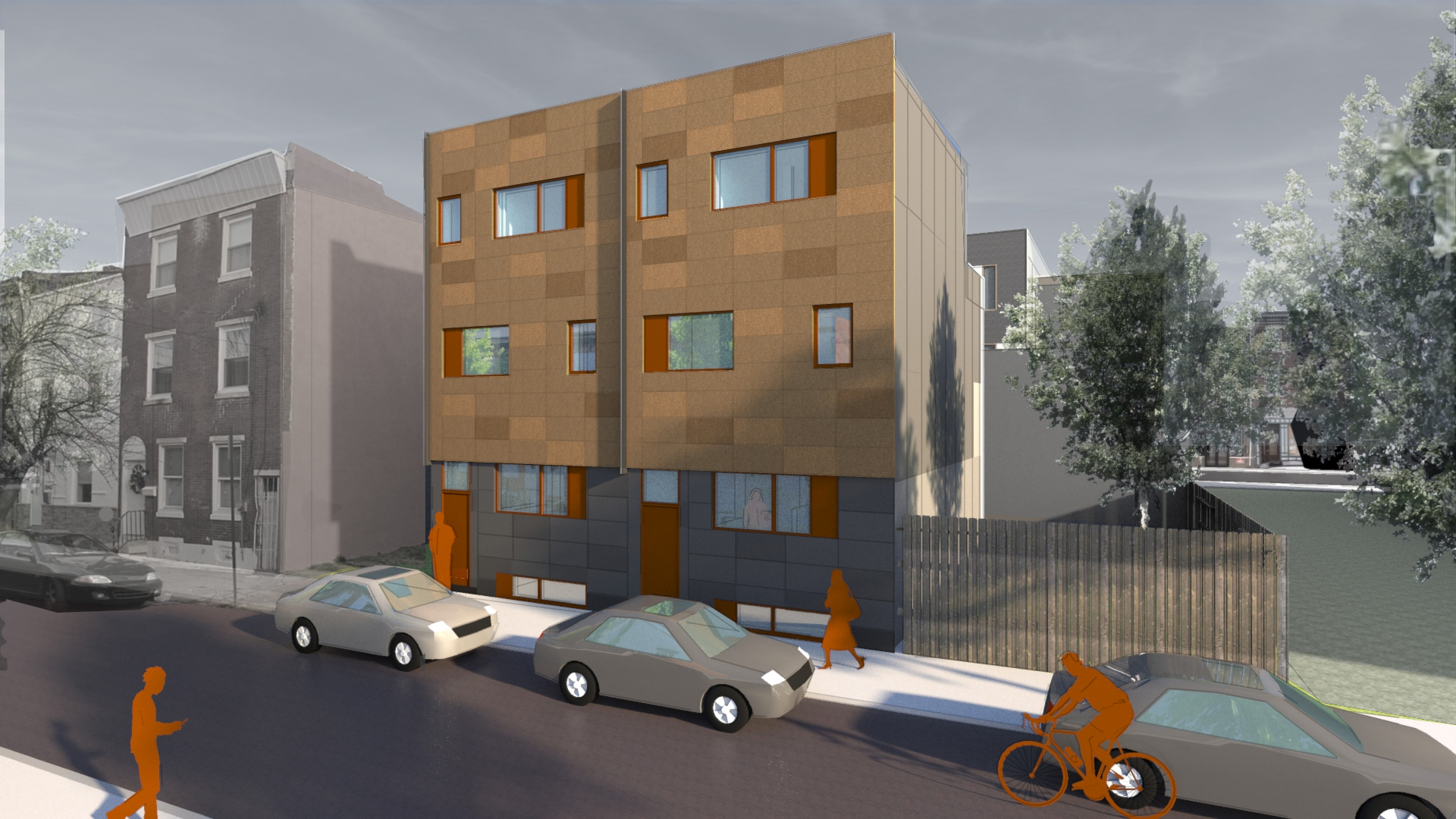
Vintage 1920's Cork Advertisements
Check out these Amazing Vintage Advertisements from Armstrong's Cork board Insulation from the late 1920's! What was said back in the roaring 20's still holds true today! The Insulating benefits from Natural Cork are simply astonishing!
The World may have changed quite a bit in the time since Armstong's Advertising campaign (as you can probably tell simply by the style of writing and language) However the message of low cost heating, cooling and extremely high levels of efficiency seem to be more applicable today than Armstong's could have ever imagined nearly a Century ago.
I love how the above sketch makes the Cork Insulated home look so warm, inviting and comfortable. Whereas the outside is an onslaught of Winter literally blowing cold and snow everywhere. Do you have your Shield from Winter ready?
This past summer, I know some of us wished we could sleep so well in the 95 Degree heat. Let alone under the blankets.
Portuguese House Boasts 100% Cork Exterior
This cork house has a simple, rectangular structure with a pitched roof, and is covered completely in cork blocks. Arquitectos Anonimos were hired to design and build his creative home. The home owner sought a building out of the ordinary, secluded, and low-cost. While unique in design, the cork facade definitely makes the home even more innovative. Built on the hillside, the home is also private from surrounding neighbors in the area. The house has six rooms, with the dining, living and kitchen on the first floor and a lofted group of bedrooms above on the second floor. It also features expansive windows, with great views and sunlight.
Low-cost meets eco-friendly? Going green just makes sense.





Cork Insulation in the White House
The picture below shows workmen installing cork insulation on the ceiling of the center hall of the third floor for thermal insulation during White House renovations in 1951. Furthermore, Harry Truman chose to renovate the Oval Office during his presidency, incorporating polished cork herringbone floor.
Cork insulation was used heavily in the United States, and was an extremely common choice for buildings until synthetic insulation was invented. At the time, the monetary cost of synthetic insulation was much cheaper and it's negative effects on the environment unknown. It's only fitting that Truman chose cork insulation; it has excellent sound isolation qualities. For a President's important and often times sensitive communications.
President Truman looks on as Workmen install Cork Insulation to the White House Ceiling